Automating the O2C Process
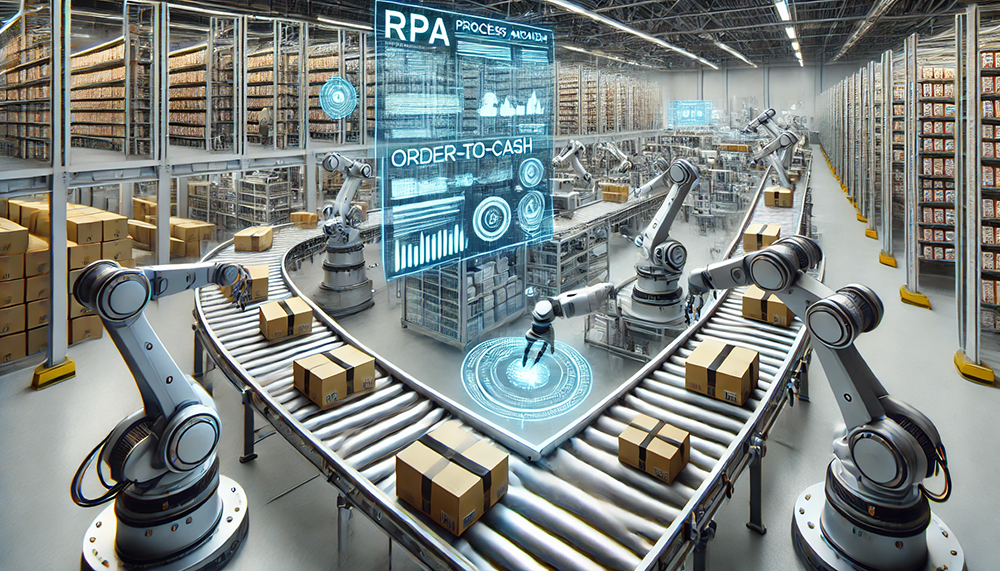
Supply Chain Wizard partnered with a global client in the pharma supply chain, where the client’s Order-to-Cash (O2C) process was crucial for order fulfillment across multiple European markets. The process involved manually processing Purchase Orders (POs) to generate sales or production orders, which was time-consuming, error-prone, and lacked scalability.
To address these inefficiencies, Supply Chain Wizard implemented Robotic Process Automation (RPA) using UiPath, streamlining operations, standardizing workflows, and unlocking significant time savings. This solution created a scalable foundation for future innovation and operational efficiency in the pharma supply chain.
Industry
Pharmaceuticals
Project
Automating the O2C Process
Client
A global client operating across multiple European markets
Objective
To demonstrate how Supply Chain Wizard automated a global client's Order-to-Cash (O2C) process using Robotic Process Automation (RPA)
Challenges
Lack of Standardization: Purchase orders (POs) varied across affiliates, creating inconsistencies that slowed the process.
Manual Effort: Employees spent hours entering data manually into the ERP system, reducing productivity and limiting capacity for higher-value work.
Error-Prone Process: Repeated manual inputs increased errors, affecting data accuracy and downstream operations.
Scalability Issues: As the business grew, the existing process struggled to scale effectively without significant resource investment.
Manual Effort: Employees spent hours entering data manually into the ERP system, reducing productivity and limiting capacity for higher-value work.
Error-Prone Process: Repeated manual inputs increased errors, affecting data accuracy and downstream operations.
Scalability Issues: As the business grew, the existing process struggled to scale effectively without significant resource investment.
Approach
Phase 1 Discovery Phase: Mapped out the existing O2C process, identified bottlenecks, and opportunities for automation through detailed process walkthroughs and flowcharts.
Phase 2 Purchase Order Standardization: Collaborated with the client to introduce a standardized PO template for all affiliates, reducing complexity and improving robot development.
Phase 3 Development and Testing: Built and tested the RPA solution using UiPath, ensuring flexibility, accuracy, and advanced exception handling for smooth execution.
Phase 4 Deployment Phase: Deployed the robot in a pilot phase, using UiPath Orchestrator on Azure Virtual Machines for centralized monitoring and management.
Phase 5 Post Go-Live and Expansion: Provided ongoing maintenance, scaled the solution across all affiliates, and monitored performance for continuous improvement.
Phase 2 Purchase Order Standardization: Collaborated with the client to introduce a standardized PO template for all affiliates, reducing complexity and improving robot development.
Phase 3 Development and Testing: Built and tested the RPA solution using UiPath, ensuring flexibility, accuracy, and advanced exception handling for smooth execution.
Phase 4 Deployment Phase: Deployed the robot in a pilot phase, using UiPath Orchestrator on Azure Virtual Machines for centralized monitoring and management.
Phase 5 Post Go-Live and Expansion: Provided ongoing maintenance, scaled the solution across all affiliates, and monitored performance for continuous improvement.
Added Value
Increased Efficiency: The robot saved approximately 15% of time per month across affiliates, freeing up time for higher-value tasks.
Improved Data Accuracy: Reduced manual errors, leading to cleaner records and smoother downstream processes. Enhanced Productivity: Employees could focus on tasks requiring judgment, creativity, and decision-making instead of repetitive work.
Standardized Operations: Introduced a standardized PO template, ensuring consistency and improving collaboration across affiliates.
Faster Processing and Response Times: The robot processed POs up to 90% faster, reducing delays and enabling quicker responses.
Digital Transformation: Reduced reliance on manual workflows, increasing operational resilience and laying the foundation for digitalization.
Scalability and Future Opportunities: The scalable automation framework opens opportunities to expand RPA into other processes for further efficiency gains.
Improved Data Accuracy: Reduced manual errors, leading to cleaner records and smoother downstream processes. Enhanced Productivity: Employees could focus on tasks requiring judgment, creativity, and decision-making instead of repetitive work.
Standardized Operations: Introduced a standardized PO template, ensuring consistency and improving collaboration across affiliates.
Faster Processing and Response Times: The robot processed POs up to 90% faster, reducing delays and enabling quicker responses.
Digital Transformation: Reduced reliance on manual workflows, increasing operational resilience and laying the foundation for digitalization.
Scalability and Future Opportunities: The scalable automation framework opens opportunities to expand RPA into other processes for further efficiency gains.
Through close collaboration with the client and its affiliates, Supply Chain Wizard successfully automated a critical part of the O2C process. This project not only improved efficiency, accuracy, and employee productivity but also established a scalable foundation for future automation opportunities.
The result is a streamlined, digitalized process that empowers the client to operate faster, smarter, and with greater consistency across their global operations.