5 Ways to Overcome Common Pharma Process Improvement Challenges
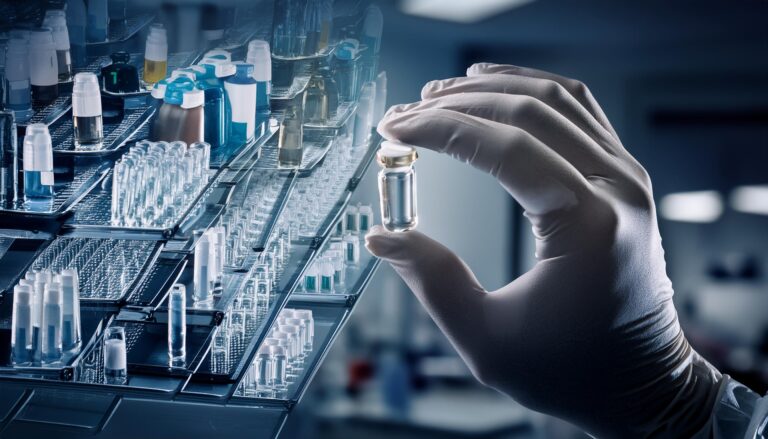
The pharmaceutical industry is a landscape of precision and complexity, where even minor inefficiencies can have a significant impact on costs, time-to-market, and ultimately patient access to critical medications. Embarking on process improvement initiatives is essential for staying competitive and meeting the ever-evolving demands of the market. However, these journeys are rarely smooth sailing.
Let’s dive into the common obstacles that pharma companies face in their process improvement efforts and uncover practical strategies to overcome them.
1. Resistance to Change: The Human Factor
Pharmaceutical companies, often steeped in tradition and regulatory compliance, can be resistant to change. Employees may be comfortable with established processes, fearing that change will disrupt their routines or threaten their job security.
The Solution:
- Clear Communication and Education: Transparent communication about the reasons behind the process improvement initiative, its potential benefits, and how it will impact employees is crucial. Address concerns openly and honestly.
- Employee Involvement: Involve employees in the improvement process. Seek their input, value their ideas, and empower them to be part of the solution. This fosters a sense of ownership and buy-in, making them more likely to embrace change.
2. Data Silos and Lack of Visibility
In many pharma companies, data is scattered across different departments and systems, creating information silos. This lack of visibility makes it difficult to identify bottlenecks, pinpoint inefficiencies, and measure the true impact of improvement initiatives.
The Solution:
- Integrated Systems: Implement a centralized data platform that brings together information from various sources, providing a holistic view of your operations.
- Real-Time Data: Invest in technologies like sensors, IoT devices, and analytics tools that enable real-time data collection and analysis. This empowers you to make informed decisions based on accurate, up-to-the-minute information.
- Collaborative Culture: Foster a culture of data sharing and collaboration across departments. Encourage teams to work together to identify problems and develop solutions based on shared insights.
3. Regulatory Hurdles: Balancing Compliance and Innovation
The pharmaceutical industry is heavily regulated, with strict guidelines governing everything from manufacturing processes to data management. While essential for patient safety, these regulations can sometimes feel like a barrier to process improvement.
The Solution:
- Regulatory Expertise: Partner with consultants like Supply Chain Wizard who have deep expertise in pharmaceutical regulations. We can help you navigate compliance requirements and ensure that your improvement initiatives align with industry standards.
- Proactive Planning: Engage with regulatory authorities early in the planning process to discuss potential changes and ensure your initiatives meet compliance requirements.
- Documentation and Validation: Document all changes to processes, systems, and data meticulously. This not only ensures compliance but also provides a clear audit trail for regulators.
4. Resource Constraints: Doing More with Less
Pharma companies often face resource constraints, whether it’s budget limitations, a shortage of skilled personnel, or limited time for implementation.
The Solution:
- Prioritization: Focus your efforts on high-impact areas that offer the greatest potential for improvement. Start with small, achievable projects to build momentum and demonstrate success.
- Leveraging Technology: Digital tools and automation can help streamline processes, reduce manual effort, and free up resources for more strategic initiatives.
- External Expertise: Consider partnering with consultants who can bring in specialized knowledge, experience, and resources to accelerate your improvement initiatives.
5. Measuring Success: Beyond the Numbers
While cost savings and efficiency gains are important, measuring the true impact of process improvement initiatives requires a broader perspective.
The Solution:
- Define Clear KPIs: Establish clear and measurable Key Performance Indicators (KPIs) that align with your strategic goals. These could include metrics like cycle time reduction, error rates, customer satisfaction, or compliance scores.
- Track Progress: Regularly monitor your KPIs to assess the impact of your improvement efforts and identify areas for further optimization.
- Continuous Improvement Culture: Foster a culture of continuous improvement where learning and adaptation are valued. Encourage employees to identify opportunities for improvement and celebrate successes.
Supply Chain Wizard is your trusted partner in overcoming these challenges and achieving lasting process improvements. Our expert consultants offer a holistic approach that combines industry knowledge, data-driven insights, and cutting-edge technology to streamline your operations, enhance quality, and drive business growth.
Contact us today to start your journey towards a more efficient and compliant pharmaceutical supply chain.
SCW’s Pro Tip
Process improvement is an ongoing journey, not a destination. By embracing a continuous improvement mindset and leveraging the right tools and expertise, you can unlock the full potential of your pharmaceutical supply chain and achieve lasting success.
For more information about SCW Consultancy Services;
For additional detail and help with Digital Maturity Assessment, please contact:
Mia Van Allen – Managing Partner – mia.vanallen@supplychainwizard.com